Published November 11, 2024
The Goal: Show that the vibration amplitudes recorded at the engine did not increase following the installation of the modified composite tail rotor blades.
Our client was contracted to review data from three accelerometers over 1100 flight load survey test maneuvers to determine if the newly installed composite tail rotor blades impacted the installed turbine engine vibratory environment. The flight test data was acquired using Dewesoft, and the flight test data was provided in 1100 files in the Dewesoft dxd format totaling 17GB. The client requested that the processing be completed within two weeks, if possible, with a go ahead to begin work immediately.
Moore Good Idea’s Vibration Processing Experience
Moore Good Ideas (MGI) was uniquely positioned to be able to rapidly complete the project. MGI has developed software applications for flight test data processing, vibration monitoring, limit checking, and reporting, and has also completed projects for monitoring rotorcraft drive system and gearbox test stands. In addition, MGI has a previously validated frequency processing library which has been used on similar data processing projects. MGI’s unique experience allows us to develop flight test analysis and reporting tools with the needs of the end user and the expectations of regulators in mind.
Project Execution
The project was assigned to two developers and work started within the week. The first challenge was to determine the most cost-efficient method to access the data. Dewesoft is able to batch export data into various third-party file formats, however it was found that the fastest and easiest method was to access the Dewesoft dxd files directly through NI’s existing dxd Data Plugin. An application was devised with a simple UI to allow an engineer to import data from the dxd files for FFT processing. Resultant data for each maneuver was summarized and compiled into NI’s TDMS file format. An SQL database was initially considered, but the development time was reduced by using the TDMS file format, and an added advantage was the ability to open and inspect the results using the TDMS Import add-on for Excel. The software UI, while necessarily basic to fit within the requested project timeline and budget, included features to organize data into two sets to be compared against each other. The UI also included features for viewing individual maneuvers, comparing those to the reference limit line, and for automating limit checking to view exceedance maneuvers and create a log file of them.
The Success
The development project was completed in under two weeks, including testing and validation, and client data processing. Validation efforts were streamlined through code reuse. The final application was delivered to the client and was able to batch import and process the 1100 maneuvers of flight load survey data in less than an hour. The application provided the required compliance artifacts to show compliance to the regulators. The data showed that the new composite tail rotor blades had produced less vibrations at the engine than the original aluminum tail rotor blades. The experimental tail rotor was certified for installation from an engine perspective.
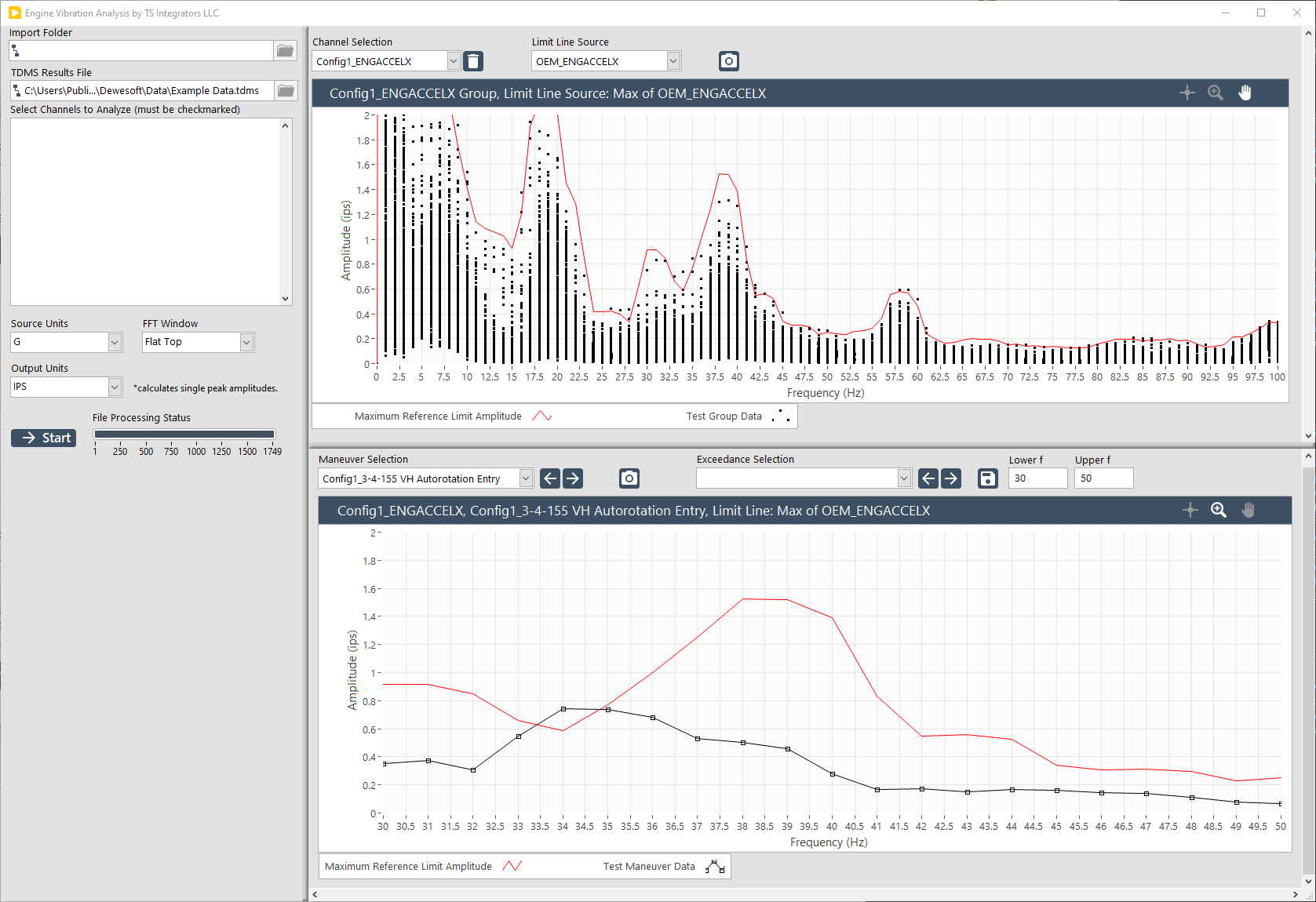