Published August 24, 2012
The Goal: Lower the cost and increase the reliability of the production of composite stiffeners
The Challenge
As the aircraft industry moves from metal to composites, they need to lower the cost of manufacturing the stiffeners used to increase the rigidity of the airframes. A composite stiffener is formed on a mandrel by applying many layers of carbon fiber fabric that have been impregnated with an epoxy resin. Because each layer is applied by hand, this process is both expensive and time consuming.
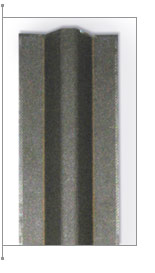
To reduce the cost and increase the repeatability of the production of stiffeners, Alliant Techsystems developed the Automated Stiffener Forming Machine (ASFM). The basic components of the machine are a carriage to move the feed system over a mandrel (1), feed rollers to hold different types of fabric (2), a tack roller to initially stick the fabric down (3), forming rollers to shape the fabric the rest of the way (4), and a cutter to end each ply (5).
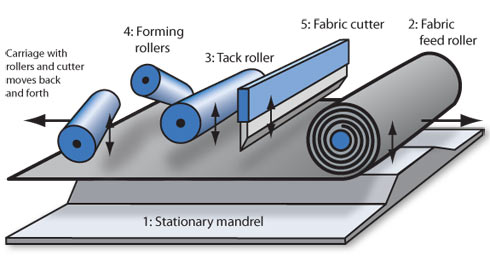
Because of the successful work we’ve done together in the past, Alliant Techsystems enlisted Moore Good Ideas, Inc. to create the automated control system that is the brain of this ingenious machine.
The Process
Creating a Design
The first step involved in making a stiffener is creating a design. All designs are stored in a library that can be edited either on the ASFM itself or on the engineer’s desktop computer. A design consists of a series of plies, each with particular start and stop positions and made of a particular material. The graphical display of the design with color coding of materials makes it easy to verify that the design has been entered correctly.
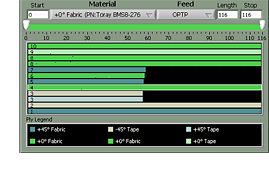
Translating a design into steps** Next, the machine needs to translate the design into a series of steps. As shown in the animation to the right, if the stiffener being made is long, the translation is straightforward. However, things start to get complicated when the stiffener is short. And they get extremely complicated when you make multiple short stiffeners at once.
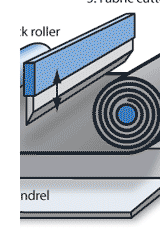
Executing the steps
Once you have the sequence of steps, you need to execute them in a reliable manner. Because Windows is not a real-time operating system, it can’t be trusted to control the rollers with the accuracy needed for the ASFM. Instead, MGI chose to use the onboard programming feature of the NI-7344 motion control board. This choice saves ATK considerable complexity and cost when compared to other real-time options. In the snippets of code shown below, we’re telling the motion board to wait for the carriage to reach a particular position and then to put the tack roller down. The LabVIEW VIs used are the same ones that normally produce an immediate response, but the motion board has been set to record commands rather than to execute them.
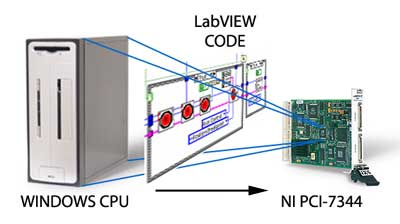
Monitoring the onboard program
The ASFM also has I/O that’s not controlled by the motion board but must be roughly synchronized with it. To control that I/O, the program running under Windows needs to keep track of the status of the onboard program.
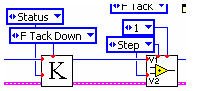
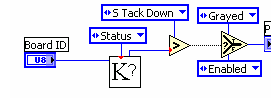
The onboard program updates two onboard variables to indicate its current status.
The Windows program polls one of the variables. In this case, it’s determining if the onboard program is in a state where it’s safe to pause.
Relieving Tension
The original machine design called for the feed roller tension to be controlled by a SmartMotor program written by the customer. “Tension” rose when it was learned that, unfortunately, the SmartMotor wasn’t up to the task. MGI was able to step up and implement a LabVIEW solution. By keeping track of the carriage and feed motion, we are able to maintain a close estimate of the feed roller diameter, and by using that information directly control the tension motor.
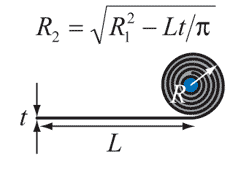
The Success
With contributions from Moore Good Ideas, Inc., Alliant Techsystems has been able to create an automated machine that reliably produces composite stiffeners with an order of magnitude less labor. Saving labor, and therefore money, is always a “Good Idea.”